Eco-Fashion 101: What is Zero-Waste Pattern Cutting?
- Ngoc Ha Thu LE
- Dec 10, 2017
- 3 min read
One of the many ways the fashion industry are harmful to the environment is how it wastes resources: 15% of fabric is lost during the cutting process – which amounts to tons of textile waste. Zero waste pattern cutting aims to eliminate this waste by incorporating every bit of the lay plan into the design; the patterns then would fit together like a jigsaw puzzle, and not a scrap of fabric would be thrown away.
An ancient mindset

Zero Waste, or at least Low Waste Pattern Cutting is not a new technique. During the period before industrialization - when fabric production is low and therefore fabric is more treasured, people from different corners of the world have come up with design that would generate the least amount of waste possible. One example would be the Japanese kimono which are essentially made up of squares.
The pattern dictate the design
One of the big difference between zero-waste pattern cutting and conventional pattern cutting is that the design process and pattern cutting process are closely entwined. The designer must be closely involved or work directly in pattern cutting – something that rarely happens in the task-specialized professional work scene. This is because 1- the designer is working within the constraint of the fabric dimension, and thus has to know of the measuments of such dimension, thinking of how to use the negative space between the patterns, and 2- even the slightest adjustment in the design can completely change the layplan and vice versa. I consider this very beneficial for the designer themselves: the better understanding you have of pattern cutting and garment construction, the better you design.
Endless possibilities
Ground-breaking ideas result from thinking out-of-the-box, and with zero-waste pattern cutting, the box is tangible and literal. The constraint of the fabric’s dimension should be viewed of as both a challenge and an opportunity; from my own experience, the negative space inspires you to invent creative way to pattern-cut, or add special features on the garment – and you will love the happy accidents. A prime example would be my first zero-waste garment, a denim kimono-inspired coat. After increasing the length of the sleeves, I am left with 10~20cm of fabric, which I decided to add on the sleeves around the armhole seam. This later on becomes both decorative and functional – as the extra strip is cut cross-grain, it’s less stiff and has more drape than the bodice & sleeve, which makes the area around the armhole more soft and comfortable. I’ve been repeating this feature on my denim designs from then.

Zero-waste pattern-cutting can be both easy-as-a-pie simple and incredibly complicated – it could be everything. On the least-challenging end of the spectrum, you have geometric patterns of t-shirts and skirts; and on the opposite end, you can incorporate curves of a fitted coat on a layplan. Pattern cutters and designers around the world come up with many different approaches. These are a few examples:
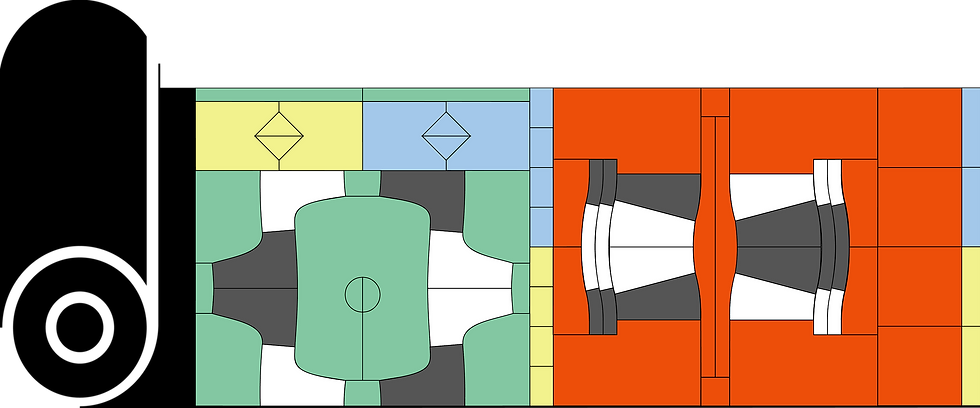
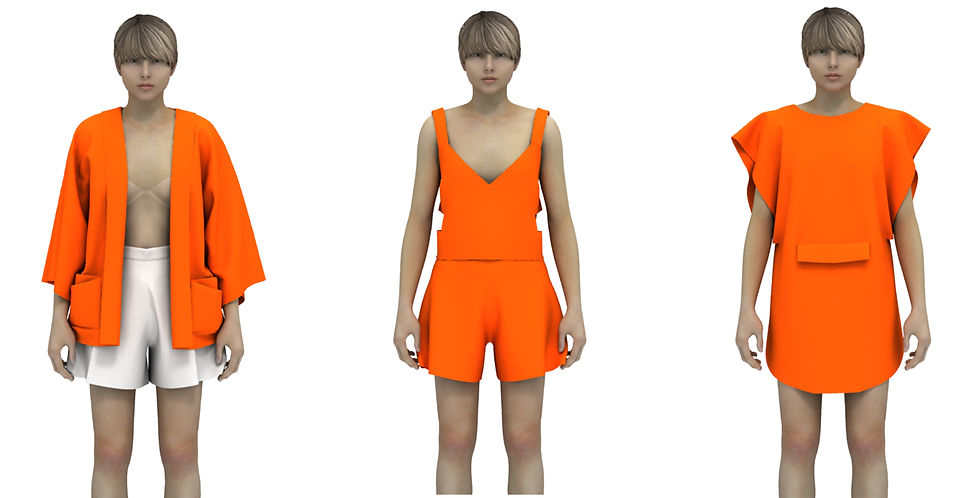
As a pattern maker specialized in CAD systems (Computer Aided Design) Mylène L'Orguilloux founded the R&D project MILAN AV-JC, which explores Zero Waste Design techniques in industrial contexts. She fit 2 or 3 garments together on a layplan; and her garment have simple, highly practical silhouette. Read more about her projects here
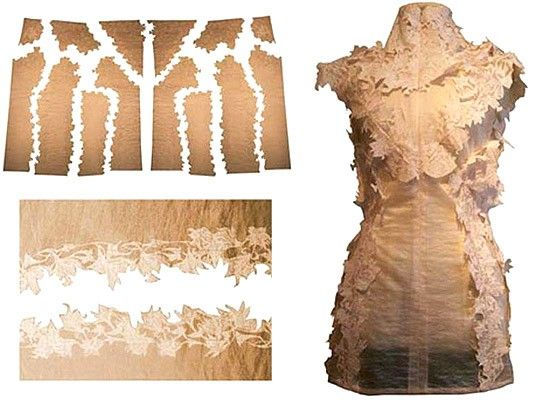
Dr Mark Liu is a fashion and textile designer focused on advancing fashion design through the use of scientific principles to traditional techniques. Mark is an acknowledged pioneer in the area of Zero-Waste Fashion design in the sustainable fashion movement in London. One of his most notable techniques is to lazer-cut the edges of the pieces to create intricate patterns that, when sewn together, become beautiful 3-dimensional features. Discover his work here
Comments